Thermocouples: details, types, usage
Thermocouples are temperature sensors used in electronic thermomenters, test meters, data acquisition systems etc & although the basic technology is straightforward there is more to them & their operation.
Data Acquisition Sensors Includes:
Thermocouple temperature sensor
Flow meters
More about data acquisition:
Understanding data acquisition
Data logging systems
DAQ systems
DAQ cards & modules
DAQ measurements
Thermocouples are widely used in many applications from simple temperature measurements to their use in data acquisition systems and a variety of other areas.
Thermocouples are the most popular type of temperature sensor because they are cheap, interchangeable, and they can measure a wide range of temperatures. The different thermocouple types have different ranges.
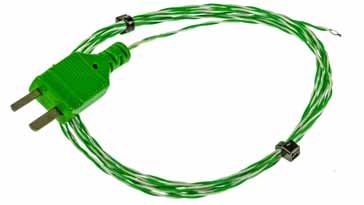
Using the different thermocouples types, it is possible to measure temperatures over a very wide range of temperatures, from below -250°C to above 2500°C. The levels of accuracy that can be achieved using these temperature sensors are also high, typically between 0.5 and 2°C and this is often sufficiently accurate for many different applications.
In view of their convenience, thermocouples are very widely used as thermocouple thermometers or electronic thermometers, in data acquisition applications, industrial temperature control systems and very many more areas where temperature sensors are needed.
Often temperature is an important measurement that needs to be made when monitoring an industrial process, and in view of their convenience and robustness, thermocouples are the idea solution. In addition to their use in data acquisition, thermocouples find widespread use in many other applications.
In one area, many digital multimeters are able to measure temperature. They have a standard thermocouple connector, and the circuitry is available to enable temperature measurements to be made. In addition to this many other uses are found for thermocouples including their use in many boilers.
In view of their simplicity, it is possible to make thermocouples in many formats. They are available as rods, probes, armoured probes, etc, and even as the bead thermocouples.
Thermocouple basics
The principle of operation of a thermocouple was discovered in 1821 by a German - Estonian scientist named Thomas Seebeck. He saw that when there was a junction between two metals, a voltage was generated that dependent upon the temperature. This is known as the thermoelectric or Seebeck effect.
The actual voltage generated by the thermocouple depends on a number of items. The first is the temperature, and another is the types of dissimilar metals used in the thermocouple. Normally the difference is small, and it may lie between 1 and 70 microvolts per degree Celsius. This means that any electronic circuitry, a digital to analogue converter in the data acquisition system for example, will need to be able to detect very small changes in voltage.
In order to connect the output from the thermocouple to a meter of some form, a further junction has to be made. In this way, there are two thermocouple junctions at different temperatures and the combined effect of these is seen by meter. In this way the overall assembly gives an output that is proportional to the temperature difference between the two thermocouple junctions.
In order to measure an absolute temperature a techniques known as cold junction compensation (CJC) is used. The second junction is held at a known temperature or static temperature. The standard method of accommodating this was to maintain the second junction at 0C for example. This could be achieved by placing the second junction in iced water to maintain it at exactly melting point.
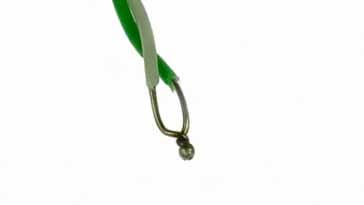
Another method is to build a compensation circuit that corrects for the difference caused by having the reference junction at a different temperature. In fact today's temperature sensor chips, designed for use with thermocouples, have this circuitry built in to them.
Often a technique known as cold junction compensation is used - essentially this technique allows the reference temperature to vary in temperature, but as this junction is likely to be much more stable, then a sensor such as a thermistor can be used to provide a basic temperature measurement and correct for any variations in the reference temperature. The thermocouple junction is often exposed to extreme environments, while the reference junction is often mounted near the instrument's location and is in a far more benign environment with much lower variations in temperature.
This approach considerably simplifies the overall circuitry required, enabling all the thermocouple compensation circuitry to be all contained within the chip.
Although it may be thought that there will be additional junctions it is found that adding intermediate metals has no effect provided that the junctions are maintained at the same temperature as the cold junction. As these further junctions are normally within the measuring instrument: the lead to the sensor junction being provided by the dissimilar metals, this is not a problem.
Thermocouple physical characteristics
Thermocouples are available in a variety of forms. They are available as bare wire bead thermocouples. Here the actual junction is exposed, and while this offers no protection, it provides very fast response times as the wires are normally thin and therefore change to the prevailing temperature very quickly.
Alternatively, thermocouples may be available as a probe. These thermocouple probes are more widely used for general purpose measuring instruments, and for applications where the temperature sensor requires protection.
Both type can be used in data acquisition systems but the type chosen for the DAQ system will depend upon the actual environment where the probe is located and whether it needs protection.
As data acquisition systems and data loggers are one of the major uses of thermocouple probes, a good selection is available.
Thermocouple types
Thermocouples have different properties dependent upon the metals or conductors used. There are several standard thermocouple types that are given designations according to the materials used.
Summary of the Different Thermocouple Types | ||||
---|---|---|---|---|
Type designation |
Materials used |
Approx temperature range (C) |
Sensitivity (uV/C) | Comments |
B | Platinum / Rhodium | 50 to 1800 | Gives same output at 0C and 42C making the minimum useable temperature around 50C | |
E | Chromel / Constantan | 68 | Normally used for cryogenic applications | |
J | Iron / Constantan | -40 to +750 | ~52 | Should not be used above 760C as a magnetic change will permanently de-calibrate the thermocouple |
K | Chromel / Alumel | -200 to 1200 | 41 | Good general purpose thermocouple, widely used and cheap |
N | Nicrosil / Nisil | 10 | Becoming a replacement for type K thermocouples | |
R | Platinum / Rhodium | up to 1600 | 10 | High cost and low sensitivity restricts the use. This thermocouple is generally used for high temperature applications. |
S | Platinum / Rhodium | up to 1600 | 10 | Very stable and therefore used as a standard of calibration for the melting point of gold (1064.43C). High cost. |
T | Copper / Constantan | -200 to 350 | ~43 | As both metals are non magnetic, this type of thermocouple is popular for applications where high magnetic fields exists, e.g. for use with electrical generators. |
These thermocouples use a variety of different materials. The ones used in the thermocouples mentioned above are all forms of metal alloys:
- Alumel Nickel 96%, manganese 2%, aluminium 2%
- Chromel Nickel 90%, chrome 10%
- Constantan Copper 55%, nickel 45%
- Nicrosil Nickel chrome silicon
- Nisil Nickel silicon
It is worth noting that thermocouple types B, R, and S are all made from noble metals and are therefore more stable than other thermocouples. However they have a low level of sensitivity (around 10 uV/C) and they are therefore normally used for higher temperatures.
Points to note when using a thermocouple
Although thermocouples offer many advantages as temperature sensors, there are a number of points to note when considering using them.
The output from a thermocouple is very low. Typically it is only a few millivolts. This makes thermocouple sensors very susceptible to noise as the thermocouple lead can act like an antenna. In particular 50 / 60 Hz power line pick-up can be a problem. To help overcome this, the two wires the go to the metal junction should be twisted together to ensure that pick-up of electrical noise is minimised. Additionally the leads should be kept as should as reasonably possible. Also the leads should not be routed through an area where high levels of electrical noise are present. Finally the design of the electrical measuring instruments used with thermocouples can incorporate filters to remove pick-up.
The fact that the output from the thermocouple is small also means that sensitive and accurate instrumentation is required. Fortunately the convenience of use of thermocouples means that there are many suitable circuits, integrated circuits and complete instruments available at competitive process.
The output from a thermocouple is not linear with temperature. Accordingly it is necessary to linearise it. Although it is possible to achieve this using hardware electronics circuits, it is normally more convenient to use software as many measurement devices use some form of processor these days.
While thermocouples consist simply of a metal junction, they are not as stable as some other forms of temperature measurement. In view of this and other inaccuracies, the overall accuracy of a thermocouple temperature measurement device is generally ~1∞C. Fortunately this is sufficient for many measurements, but it is often necessary to check the accuracy requirements to ensure that a thermocouple can meet the needs for the temperature measurement before proceeding.
Thermocouples are widely used as temperature sensors in many applications. Although data acquisition and industrial process control make extensive use of them, they are also incorporated in many stand alone thermometers.
The type of thermocouple that is most widely used is the K type thermocouple. This is also the type that is used in most portable instruments as it provides a high output over the ranges most widely used. Nevertheless other types of thermocouple are still used in other applications where more specialist requirements exist.
Thermocouples have many advantages when compared to other forms of temperature measurement. They are small in size, and this makes them fast to respond to temperature changes. Thermocouples also offer a wide temperature range, and they are also good for measuring high temperatures. Finally they are comparatively cheap to manufacture.
When combined, these advantages make thermocouples an obvious choice for many temperature sensor applications from data acquisition systems and data loggers to electronic thermometers and the like.
Written by Ian Poole .
Experienced electronics engineer and author.
More Test Topics:
Data network analyzer
Digital Multimeter
Frequency counter
Oscilloscope
Signal generators
Spectrum analyzer
LCR meter
Dip meter, GDO
Logic analyzer
RF power meter
RF signal generator
Logic probe
PAT testing & testers
Time domain reflectometer
Vector network analyzer
PXI
GPIB
Boundary scan / JTAG
Data acquisition
Return to Test menu . . .